In today's life, metal cans have become an integral part of our lives. Food cans, beverage cans, aerosol cans, chemical cans, oil cans and so on everywhere. Looking at these beautifully made metal cans, we can not help but ask, how are these metal cans made? The following is Chengdu Changtai Intelligent Equipment Co., Ltd. on the metal tank manufacturing and production process of a detailed introduction.
1.Overall Design
For any product, especially packaged products, appearance design is its soul. Any packaged product, not only to maximize the protection of the contents, but also in the appearance of the customer's attention, so design is particularly important. Design drawings can be provided by the customer, or can be designed by the tank factory according to customer requirements.
2.Prepare Iron
The general production material of metal cans is tinplate, that is, tin plating iron. The content and specification of tinned material shall meet the quality requirements of National Tinned Steel Plate (GB2520). Generally, after confirming the order, we will order the most suitable iron material, iron variety and size according to the nearest layout. Iron is usually stored directly at the printing house. For the quality of iron materials, the common method of visual inspection can be used to look at the surface method. Whether there are scratches, whether the line is uniform, whether there are rust spots, etc., the thickness can be measured by micrometer, hardness can be touched by hand.
3. Customization Of Metal Cans
Customized metal cans can be made according to the design drawings, can automatically adjust the diameter, height and speed of the can.
4. Typesetting and Printing
It should be noted here that the printing of iron materials is different from other packaging printing. Not cutting before printing, but printing before cutting. Both the film and the layout are arranged and printed by the printing house after the printing house has passed the printing house. Usually, the printer will provide a template to follow the color. In the printing process, attention should be paid to whether the printing color can be in accordance with the template, whether the color is accurate, whether there are stains, scars, etc. These problems are usually caused by the printer itself. There are also some canneries that have their own printing plants or printing facilities.
5. Iron Cutting
Cutting iron printing material on a cutting lathe. Cutting is the relatively easy part of the canning process.
6 stamping: is the iron press on the punch, is the most important part of can. Often, a can can be done through more than one process.
The general process of the world cover two cans is: cover: cutting - flashing - winding. Bottom cover: cutting - flash - pre-rolled - winding line.
Heaven and earth cover bottom process (bottom seal) tank process, cover: cutting - flashing - winding tank: cutting - pre-bending - cutting Angle - forming - QQ- punching body (bottom buckle)- bottom seal. The underlying process is: openness. In addition, if the can is hinged, then the lid and the body of the can each have a process: hinging. In the stamping process, iron material loss is usually the greatest. Attention should be paid to whether the operation is standard, whether the product surface is scratched, whether the coil has batch seam, whether the QQ position is fastened. A lot of trouble can be reduced by arranging to confirm the production of large sample and producing according to the confirmed large sample.
7.Packaging
After stamping, it's time to get into the finishing touches. The packaging department is responsible for cleaning and assembling, packing into plastic bags and packing. This is the final step of the product. The cleanliness of the product is very important, so the work should be cleaned before packing and then packed according to the packing method. For products with many styles, the model number and case number must be put away. In the process of packaging, we should pay attention to quality control, minimize the flow of unqualified products into finished products, and the number of boxes must be accurate.
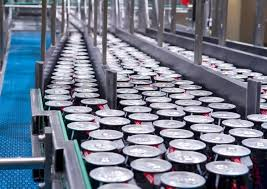
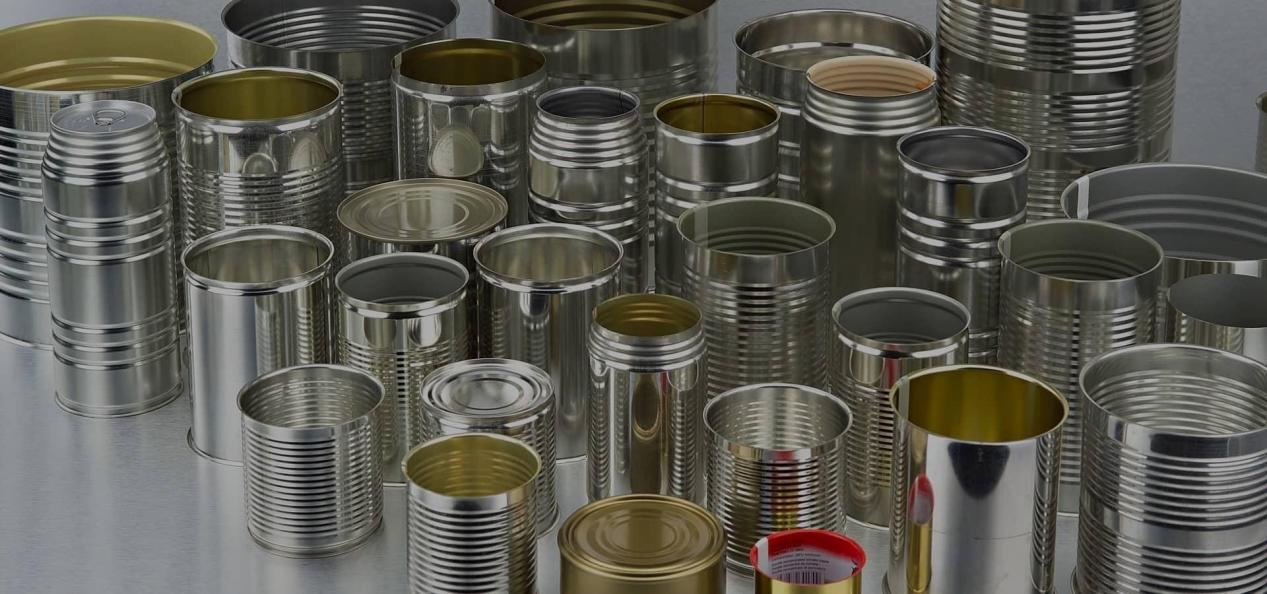
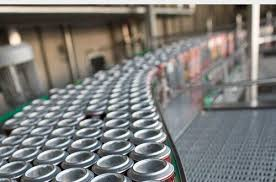
Post time: Nov-30-2022